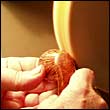 |
|
Poul Ilsted, pipe maker, Svendborg
Poul Ilsted is recognised to be one of the World's best pipemakers but rarely shows himself. He has now for the past 30 years been producing these wooden jewels.
After a long time of persistent importunities Poul was finally met with sympathy at the pipemaker Erik Nørding, who sold him 3 pieces of briar and offered tips for their finishing as well. After 2 weeks, when Poul showed his finished work to the ingenious pipemaker, Nørding gave him a brief, yet important praise: Well done. And thus Poul Ilsteds future career was carved out.
Nobody ever taught him how to model a pipe. He learned by doing. Poul read everything about pipes that he could get his hands on, he studied and designed shapes. Quote: I had the ambition to make pipes, which were more beautiful than were those of the illustrated catalogues.
In his new occupation he first worked 2 years for Nørding, then 2 years at the newly founded pipe factory, Svendborg, and finally an additional year with Nørding followed by nearly 2 years at W. Ø. Larsen in Copenhagen.
A decade ago known as Mr. Bulldog
After his apprenticeship, Poul Ilsted became self-employed. In the beginning he became known for his Bulldogs (of all possible and impossible shapes and sizes), which 10 years ago gave him the nickname, Mr. Bulldog, among connoisseurs e.g. in Germany. I have always been devoted to the Bulldog, he stresses.
He did not really become world-famous, however, until he started making his unbelievably perfect-faceted pipes. Without envy even his most skilled colleagues grant Poul the title of honour: The Facet Master. Especially the finishing of a strongly curved pipe with faceted bowl and shank is, in his opinion, particularly difficult and time consuming. And if it has to be sandblasted because a small unevenness disturbs its shape, the obtainable price for the pipe will hardly make up for the many hours it took to make it.
The pipes are all manifests of excellent workmanship. Poul hates scamped work and readily admits that he is a perfectionist when it comes to pipemaking. He only uses Corsican briar from the east side of the Mediterranean island: It is particularly densely grained and has only few defects.
In Germany, chief market next to Japan and Denmark, a simple sandblasted Ilsted costs nearly £ 200 a polished specimen of supreme quality will roughly amount to £ 900.
For stem bands, inserts and accents the Dane uses gold and silver, ebony, Brazilian rosewood and buffalo horn from South American longhorn cattle. He doesnt work with ivory anymore, but prefers to experiment with new materials like the deep blue precious stone, lapis lazuli.
The mouthpieces are usually made of black ebonite and are (of course) hand-made. Cumberland also comes in use. Artificial amber, though, is not to his liking, as it develops toxic vapours when worked with. Only once he made a pipe with a mouthpiece of genuine Bernstein, as: Bernstein is not necessary it is too hard to bite on. However, this does not prevent Poul from having a passion for the fascinating structure and biblical age of this material.
No raptures over filter pipes
When talking about filter pipes, Poul shows no enthusiasm about the idea on the contrary. The native of Funen occasionally makes them to order but doesnt value this type of pipe: The design suffers and the smoking quality is poorer, as the pipes easily get wet when smoked.
The master makes about 170 pipes per year not even one tenth of them are sandblasted. Is it possible to live by that? It is enough to exist, claims Poul.
Undoubtedly he can be counted among the most officious collectors of his own noble pieces. He has made over 50 fabulously beautiful and unique pipes for himself. I only take the best. He also owns a Dunhill, which looks quite exotic among the exquisite collection, where one Bulldog is particularly conspicuous: It is ornamented with a silver ring densely interwoven with mysteriously shining strings of copper. With a special metalwork technique the primitive forge is right next to the workshop Poul mixed silver and copper. In Germany he sold only 4 such ingeniously produced specimens. The process takes very long time, and I get too little for my effort.
Ilsteds own pipes look very well cared for although some of them are quite old. How is that possible? I always polish my pipes with a dry cloth when I finish smoking them. This makes them even more beautiful, he finally answers. And there seems to be a twinkle of laughter in the corner of the intelligent brown eyes of this unconventional man.
|
|
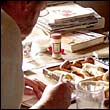 |