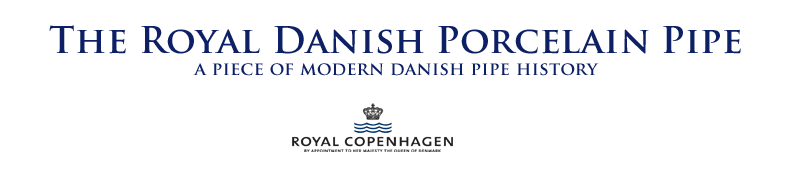 |
By Jakob Groth
Pipes & Tobacco magazine #3, vol. 7, Fall 2002 published an extensive and excellent article by pipe expert Ben Rapaport about the history of pipes made of porcelain. From Danish point of view one thing was missing: The history of the modern porcelain pipe, The Royal Danish Porcelain pipe. This article deals with this piece of the pipe history.
|
|
|
|
The history of The Royal Porcelain Factory
One of the oldest and most famous Danish trademarks is the three blue waves of The Royal Porcelain factory. This trademark has for centuries been synonymous with porcelain objects of the highest quality by almost every adult Dane. The purpose of this article is to describe a little piece of interesting resent Danish Pipe history which the Royal Porcelain Pipe is a part of.
At the same time it is a piece of modern history of the porcelain pipe which has been made for centuries.
The increasing trade with Asia in 1600 century had made the Europeans very interested in the Chinese “white gold” the porcelain. For several decades European chemists tried to copy the Chinese secret and in 1709 in Dresden, Germany and acceptable result was achieved.
In 1775 the Royal Porcelain factory was started under protection of Queen Julianne in the center of Copenhagen. The three blue waves symbolize Denmark’s three biggest and are painting and the white background color was chosen already at that time.
The main products of the factory were various distinguished (dining) services for the royal house and the nobility and often given as present for other royal families.
In middle of the 1850’s Danish porcelain production flourished and in 1851 the factory qualified for World Expo for the first time.
In 1849 Denmark had had new constitution and many royal companies were privatized, the Royal Porcelain Factory from 1868. In 1882 the company was bought by a sister porcelain company, but continued under the name, now situated in Frederiksberg (outer Copenhagen at that time) until few years ago.
At the end of 1800’s the two united companies prospered from the growing wealth of the increasing upper and middle class. The number of products increased and techniques and designs was constantly developed. Many artists and technicians were involved. In 1889 once again the factory is showing its products at a World Expo and wins the Grand Prix which secures an international breakthrough.
The very popular Christmas plates have been made since 1895 and are still produced.
The technical development and the collaboration with different artists continues in 1900-century. New artistic movements as art nouveau were included.
After II. World War the Royal Porcelain factory became one of most esteemed makers of Danish Design with retailing shops on the most fashionable streets all over the World.
Today the company has merged with a number of other companies producing handicraft, Royal Copenhagen, which again has merged with Scandinavian companies, for example several famous Swedish glassworks, under the name Royal Scandinavia.
|
|
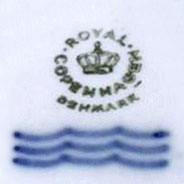 |
|
|
|
The birthday present
And what does that have to do with pipes?
Well, for a period of about 15 years, from 1970 to mid 80’s, the Royal Porcelain factory produced some very interesting and unique porcelain pipes with very special smoking characteristics.
In 1969 the Danish King Frederik 9 celebrated his 70 anniversary. On the Royal Porcelain factory they considered what to give the King as present. Frederik 9 was known as an enthusiastic pipe smoker and a board member of company suggested that the factory should make a porcelain pipe similar to the modern briar pipe.
Two pipes and a tobacco jar were created and presented to the King. The making of these two pipes turned out so well that the factory decided to start a mass production of porcelain pipes.
The year after the factory introduces a series of 8 porcelain pipes. The shapes were based in traditional, classic (English) shapes such as Billard, Zulu, Bent and so on, but the shapes were rounder and softer due to the nature and production method of porcelain. An exception from the classical shapes was the spectacular Golf Ball.
The pipes soon got popular and widespread in Denmark. The factory advertised a lot and organized “smoking-introduction-evenings” with introduction of the new pipes round the country. And the grand old man of Danish pipe smoking, Denmark’s pipe writer no. 1, P. C. Olrik, wrote enthusiastic and warmly about the in his magazine Stop and his books. He recommended that every pipe smoker should have at least one porcelain pipe on his (or her) collection.
|
|
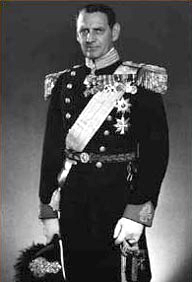 |
|
|
|
Method of production
The production of the pipes was quite complicated and the factory had to make many adjustments along the way. The pipes had to be functional and smokeble if they were to be sold.
First step in the process of the production was that a designer created a model/shape in natural size.
Then the model/shape was copied on the factory in a 15-17% oversize model. The oversize was because the porcelain is shrinking when it is burnt in the oven.
A casting mould was made as a master. From technical reasons the shank and the bowl was cast separately and then assembled.
The casting form was filled with liquid porcelain, which was poured out after 4 minuets. A hollow shell was left the pipe bowl.
The bowl and shank was burnt in an oven by 900 degree Celsius.
Then the decorators took over. The bowl was decorated with the traditional blue color (or none) in classic pattern.
Important steps were yet to come: Mounting of Teflon as mortise in the mouthpiece, mounting of a reverse metal tenon from the shank into the mouthpiece, a small silver ring on the shank and finally mounting of a polished mouthpiece.
Click a thumbnail to enlarge... |
|
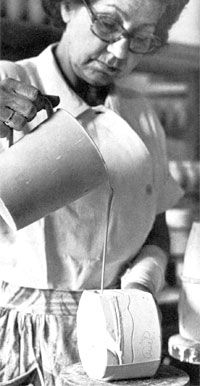 |
|
|
|
Making porcelain pipes is not that easy
In the beginning the factory had quiet a lot of problems with the production, basically because the pipes were hollow, so they would not be overheated.
Making a tenon so it didn’t get loose or to tight was problem. A briar and vulcanite (or acrylic) expand very well together but the porcelain does not expand very much when it gets hot. So the factory tried to make a mortise of Teflon and a metal tenon in the stem.
After some complaints from customers (the stem would get to loose and the bowl fall off), they made it reverse: tenon in the shank and mortise in the stem. That worked. In the first year they had problems with glazing the bowls entirely, so the very early pipes have a small hole in the glaze in the bottom. But all the problems were overcome and after 2 years the pipes were smoking satisfactory.
Click a thumbnail to enlarge... |
|
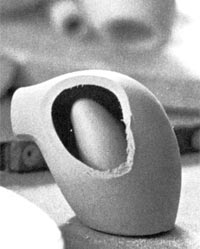 |
|
|
|
Smoking qualities
How are the Royal Porcelain pipes to smoke from? Well, it is a fine experience to smoke them, but quite different from our traditional briars.
The porcelain does not add any taste at all to the tobacco unlike briar. The porcelain pipes give a very pure taste of the tobacco you are enjoying. Furthermore they very easy to clean you dish wash them! Remove the stem, take an old toothbrush, hot water and soap, clean it and the pipe is like new.
The hollow bowl makes the smoke cool and pleasant. This all does that the pipes are very good when you are testing new tobaccos. It is very comfortable to hold in your hand, but have to hold it in the hand most of the time because it is too heavy to hold in your mouth constantly.
If you drop it on a stone floor, you don’t have to pick it up, you sweep it! The biggest disadvantage is that the tobacco chamber is some what conical because of casting process. This means the last third of the tobacco can get hot and moist.
If it does scrap it out. Anyway the last part of tobacco has worked as filter and does not really taste well neither in a briar.
|
 |
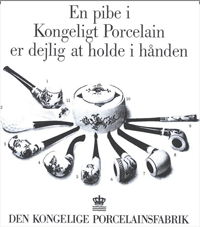 |
|
|
|
Shapes
In the beginning the factory introduces a series of 8 shapes, based on traditional English shapes, such as Billard, Apple, Bent and Zulu, but rounder and softer in the shapes than briars, due to the casting process and nature of porcelain. An exception from the classics was the Golf Ball, which must appeal to all pipe smoking golfers.
They also introduced a elegant cigarette holder and a tobacco jar. It was not very practical because it didn’t hold tight and the tobacco dried out.
After a couple of years they wanted to expand the number of shapes and this time they should be Danish shapes. As mentioned before the Royal Porcelain factory has a long tradition of collaboration with individual designers, a concept also known from other design oriented hand crafting industries such as furniture and glass. Also the leading Danish pipe factory Stanwell has used shapes created by individual pipe makers with Sixten Ivarsson as the foremost example. This was one of the ways the idea of Danish Design originated.
Therefore the factory invited a number of individual internationally reputed pipe makers to a contest of shapes and a number of Danish “pipe personalities” to judge among the suggested shapes.
Click a thumbnail to enlarge... |
|
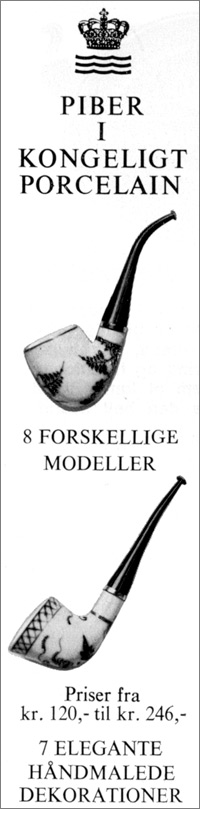 |
|
|
The design contest
In autumn 1971 the factory launched the contest. The invited pipe makers were among the leading and most prominent Danish pipe makers at that time, from both the so called 1. and 2. generation of makers in Denmark: Anne Julie, Emil Chonowitsch, Jess Chonowitsch, Poul Hansen, Gert Holbek, Lars Ivarsson, Sixten Ivarsson, Svend Knudsen, Ib Loran, Jørn Micke and Karl Erik Ottendahl.
After 3 month, at the end of 1971, the contesting shapes were handed in anonymously, all together 49 shapes. The judges. H.Dan-Christensen, pipe writer P. C. Olrik, ceramist Nils Thorsen, leading engineer from the factory L. Lautrup Larsen and art professor Erik Herløw unanimously choose 5 shapes:
1. prize: shape by Micke
2. prize: shape by Loran
3. prize: shape by Micke
A shape by Lars Ivarsson and one by Anne Julie were bought too. 1. prize was 3000 Danish kroners (app. 450 $), 2. prize was 2000 kroners and 1000 kroners for the last three each. Both Micke and Ivarsson had had the idea of coloring their shapes white to make it easier to abstract from the structure and grain of the wood.
For 2 years the technicians of the factory worked before a series of new shapes were introduced
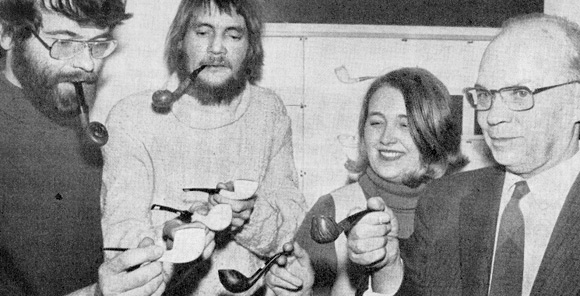
Lars Ivarsson, Jorn Micke, Anne Julie, Ib Loran |
|
|
|
|
New shapes Danish Design
8 new shapes were introduced: The 3 prizetakers from the contest, Lars Ivarsson’s shape and 4 new shapes from Micke. The collaboration must have been good between the factory and Micke and his shapes very suitable for reproduction in porcelain.
Micke (who passed away Spring 2005) was a student of Sixten Ivarsson. He wanted to stay out of the limelight and moved to the island of Bornholm, where he lived for the rest of his life. He only produced about 20 very high grade and expensive pipes each year, which were sold in USA (Iwan Ries), Japan and later on Switzerland. He preferred to talk about his pastime and passion of painting and not his pipe making.
At the same time the factory introduced an additional new surface, besides the totally white and the blue-on-white glace. The new surface was brown and gold, a more ceramic surface very beautiful.
Many of the new shapes are very hard to find today, not to mention pipes with the new surface.
|
|
Micke
|
|
|
|
End of production
After about 15 years the factory ended the production in the middle of the 80’s.
The pipes had been selling okay but the market was decreasing. (Pipe) smoking had a difficult time all over the World. Many Danish pipe makers had problems with selling their pipes too luckily not any more, since the pipe boom in the middle of the 90’s.
|
|
|
|
|
|
How to get a Royal Porcelain pipe?
If you are a passionate pipe collector and smoker, you should try one of these pipes. It’s an interesting alternative to the briar pipe at least occasionally just like at meerschaum pipe. In antique shops you can sometimes find one.
If you are really lucky you can also find single ones on flea markets or on estate pipe web sites. The pipes are seldom cheap. Already back in ’74 the white ones cost 165 Danish kroners (ca. 25 $), the blue hand painted 260 kroners (40 $) and the golden/brown 285 kroners (43 $) in the Danish pipe shops and tobacconists but after all they were royal pipes.
Jakob Groth
|
|
|